Why Resin FRP Material Is Changing Construction Forever
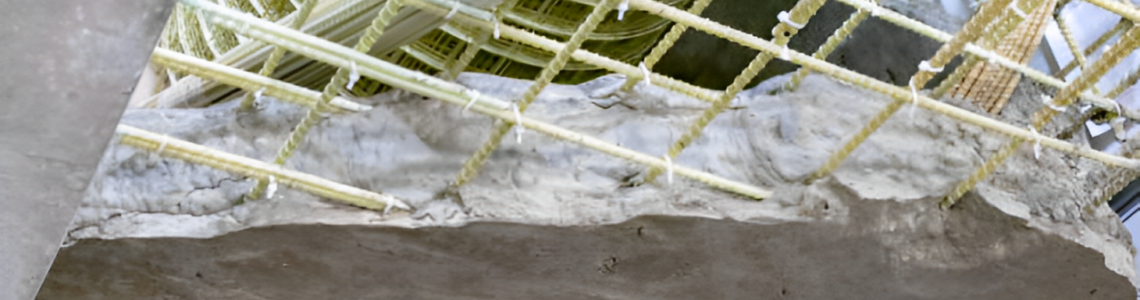
If you're still using traditional steel for structural reinforcement, now it's time to rethink your strategy. Steel has long been the standard, but everyone knows that it rusts, it’s heavy and also needs high maintenance. That’s where resin frp material steps in as a modern alternative.
More and more engineers, builders and manufacturers are switching to FRP rebar, especially those made using high-performance FRP resin. It’s not just a replacement for steel—it’s an upgrade that solves real-world problems like corrosion, weight, and long-term durability.
Let's look into why resin, and specifically resin-based FRP rebar, is going to be the backbone of modern infrastructure - and why it is important to purchase your FRP resin from the right supplier in order to get the intended performance and results.
Why Resin FRP material Is the Game-Changer
The construction world is shifting. Sustainability and long-lasting durability are now more critical than ever. This is where FRP materials company solutions powered by resin frp material are making headlines.
Traditional steel rebar corrodes over time, especially in humid or marine environments. The corrosion diminishes the strength of the structure, resulting in expensive repairs, safety concerns, and stability issues. However, FRP rebar, manufactured from advanced FRP resin material, is a proven and sustainable alternative.
Top Benefits of resin frp material in Construction
Here’s what makes FRP rebar, produced using top-grade rebar epoxy, a superior choice for modern construction projects:
1. Unmatched Corrosion Resistance
FRP products manufactured from high-quality FRP resin never rust. The resin frp material is the best possible protection against moisture, chemicals, and salt. Protection provides a better-life cycle performance in the harshest environments.
2. Thermal Compatibility
Steel and concrete expand at different rates, which causes cracks. resin frp material, however, has a thermal expansion rate that matches concrete, offering better structural harmony across temperatures.
3. Lightweight Yet Strong
Don’t let the lighter weight fool you—FRP rebar holds its ground. Rebar made using high-performance resin is easy to handle and transport. FRP rebar will reduce the expense of labor while maintaining structural integrity. The right FRP resin ensures strength without added bulk.
4. Non-Conductive and Non-Magnetic
In sensitive environments like MRI rooms or substations, FRP products shine. They don’t conduct electricity or interfere with magnetic signals—qualities that originate from the resin epoxy they’re built with.
5. Long-Term Savings
With fewer replacements and lower maintenance, resin-based FRP rebar helps manufacturers provide construction materials that are affordable and resourceful in the long run.
A Quick Look Into the Manufacturing
Here's a quick manufacturing process overview, even if you are not an engineer this is useful to understand as the quality of FRP resin is critical to the strength and durability of the end product.
1. Saturation of Fiberglass Strands
Fiberglass strands are fully saturated in FRP resin to provide a full bond for strength and performance.
2. Shaping & Curing
The impregnated fibers into bars, curing it in our controlled area, in the curing process the resin epoxy solidifies, locking in durability.
3. Ribbed Surface Formation
The surface is textured for better concrete bonding—a vital step enabled by the flexibility and viscosity of the resin frp material.
4. Cooling and Packaging
Once set, the bars are cooled, cut, and prepped for distribution.
At every stage, the role of FRP resin is foundational—it determines everything from tensile strength to environmental resistance.
Where Is Resin-Based FRP Rebar Used?
The resin frp material is extremely versatile and can be used in a range of industries because of its flexibility, durability, and inherently high corrosion resistance. Also note that we at MB Enterprises provide the high-quality FRP resin, the base material that manufacturers use to make these FRP based products.
Common applications include:
- Concrete Reinforcement: In bridges, buildings, and parking structures, where FRP rebar—manufactured using resin frp material—offers improved corrosion resistance compared to steel.
- Marine Infrastructure: Given its durability in saltwater, FRP rebar made using FRP resin is commonly used in docks, seawalls, and piers.
- Structural Rehabilitation: Resin-based fiber reinforced polymer (FRP) rebar is typically used to restore strength in older buildings while providing additional load-carrying capacity (strengthening) without changing their structure.
- Tunnel Construction and Mining: In underground tunnels and chemical processing plants, there exists high-moisture or chemically aggressive environments where resin-based FRP provides products that maintain their resilience and strength in demeaned stress conditions.
FRP Rebar vs. Steel: A Straightforward Comparison
Feature | Resin FRP Rebar | Steel Rebar | ||
Corrosion Resistance | Excellent | Rust-prone | ||
Weight | Lightweight | Heavy | ||
Thermal Compatibility | Matches concrete | Risk of cracking | ||
Conductivity | Non-conductive | Conductive | ||
Maintenance | Low-cost, long-term | High and recurring |
Resin-based rebar epoxy offers a stronger and more adaptable solution, especially when sourced from trusted epoxy resin manufacturers.
Why resin Frp material Is the Future of Reinforcement
As infrastructure evolves, there's growing pressure on industries to offer construction solutions that are high-performing, eco-conscious and cost-effective. And resin frp material checks all three boxes.
By switching from steel to FRP-based reinforcement made with high-quality FRP resin, manufacturers can:
- Reduce material weight
- Eliminate rust-related failures
- Lower long-term maintenance costs
- Support more sustainable construction practices
Partner with MB Enterprises – Leading Supplier of FRP Resin for Industrial Use
Whether you're in product development or materials procurement, choosing the right epoxy resin suppliers in India is a key step toward meeting future industry standards.
Partner with MB Enterprises – Leading Supplier of FRP Resin for Industrial Use. If your business is involved in the manufacturing of FRP rebar, panels, coatings, or other FRP products, the quality of your raw resin matters more than ever.
MB Enterprises, one of the trusted epoxy resin manufacturers in India, offers you high quality FRP resin that you can use for your industrial needs. We are proud to provide the highest quality resin frp material engineered to meet the performance requirements for durability, resistance to chemical attack, strength-to-weight optimisation. Being one of the experienced epoxy resin suppliers in India, we understand the needs of today’s construction and the quality raw materials needed. Let us support your manufacturing process through raw materials you can trust.
FAQs
1. What resin is used in FRP?
The most common resins used in FRP products are epoxy resin, polyester, and vinyl ester. Among these, epoxy-based resin FRP material stands out for its superior strength, chemical resistance, and long-term durability.
2. What does FRP stand for?
FRP stands for Fiber Reinforced Polymer. It’s a composite material made by combining a polymer resin with reinforcing fibers like glass (GFRP), carbon (CFRP), or aramid. The FRP resin binds the fibers together, giving the final product its strength and resilience.
3. What is FRP used for?
FRP materials are used across industries for making lightweight, corrosion-resistant products such as FRP rebar, structural components, water tanks, grates, panels, and more. In construction, FRP rebar made using resin FRP material is often used to reinforce concrete structures, especially in harsh or marine environments.
4. What is fiberglass resin used for?
Fiberglass resin is used to bond glass fibers into a solid, durable structure. It’s commonly applied in automotive repair, boat building, and construction materials.
5. What are the 4 main types of FRP?
The four main types of FRP based on reinforcement fibers are:
- GFRP – Glass Fiber Reinforced Polymer
- CFRP – Carbon Fiber Reinforced Polymer
- AFRP – Aramid Fiber Reinforced Polymer
- BFRP – Basalt Fiber Reinforced Polymer
Each type offers different benefits, but GFRP made with resin FRP material is most widely used in construction.
6. Is FRP waterproof?
Yes, FRP is inherently waterproof. That’s why resin-based FRP is ideal for marine structures, tunnels, and underground installations.
7. What is the function of FRP?
The main function of FRP is to provide lightweight yet strong reinforcement. It’s used to enhance structural integrity while resisting corrosion, thermal stress, and environmental damage.
8. What is the chemical name for FRP?
FRP itself doesn’t have a single chemical name because it's a composite material. However, the resin component often involves epoxy resins (chemically derived from epoxides) or unsaturated polyester resins, depending on the application.
9. What is the price of FRP material?
The cost of FRP material varies depending on the type of fiber, resin used, and application. While resin FRP material may cost more upfront than steel or basic polymer composites, it offers long-term savings due to its durability and low maintenance.
10. Is FRP material strong?
Absolutely. FRP material offers a high strength-to-weight ratio, often outperforming steel in specific use cases. When manufactured using quality FRP resin, it can handle significant loads while being lightweight and corrosion-resistant.
11. Why is FRP so expensive?
While FRP products can be more expensive than traditional materials initially, the cost reflects the advanced resin technology, long-term durability, and performance benefits.
12. Is FRP UV resistant?
Yes, when made using UV-stable FRP resin, it can resist damage from prolonged sun exposure. This makes them suitable for outdoor structures, façades, and marine applications.
13. Can you paint FRP?
Yes, FRP surfaces can be painted but proper surface preparation is essential. Using compatible primers and coatings helps the paint adhere well to the FRP coating, which is typically non-porous due to the resin epoxy layer.
Leave a Comment